Spray Drying for Chemicals: Boosting Efficiency and Quality in Manufacturing
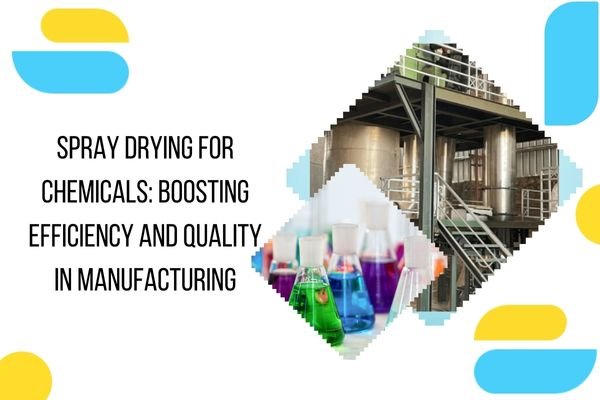
Spray Drying for Chemicals: Boosting Efficiency and Quality in Manufacturing Spray drying is a critical process in the chemical industry, transforming liquid solutions into dry powders with precise control over particle characteristics. This technology is widely used in the production of catalysts, detergents, ceramics, and specialty chemicals, where consistency and efficiency are paramount. Key Advantages of Spray Drying in Chemical Manufacturing Enhanced Product Stability: The rapid evaporation in spray drying prevents thermal degradation, preserving the chemical integrity of sensitive materials. Precise Particle Control: Atomization and drying parameters can be adjusted to achieve the desired particle size, shape, and moisture content. Scalability and Continuous Processing: Unlike batch drying, spray drying supports large-scale production with minimal downtime. Improved Flow Properties: The resulting powders exhibit excellent flowability, making them ideal for downstream processing such as tablet compression or blending. Customization for Various Applications: Spray dryers can be configured for specialized needs, such as agglomeration, encapsulation, or microencapsulation of active ingredients. Optimizing Spray Drying for Maximum Efficiency Selecting the Right Atomizer: Rotary atomizers are preferred for fine particle sizes, while pressure nozzles offer higher throughput for coarser particles. Fine-Tuning Airflow and Temperature: Proper inlet and outlet temperature control ensures uniform drying while preventing overheating or incomplete drying. Controlling Feed Rate and Solids Concentration: Maintaining a consistent feed rate and appropriate solid content optimizes yield and minimizes product loss. Ready to Optimize Your Spray Drying Process? If you’re looking for expert guidance on maximizing efficiency, improving particle control, or troubleshooting spray drying challenges, our team is here to help. Contact us today to discuss your needs and discover how our advanced spray drying solutions can elevate your manufacturing process.
Spray Drying in the Pharmaceutical Industry
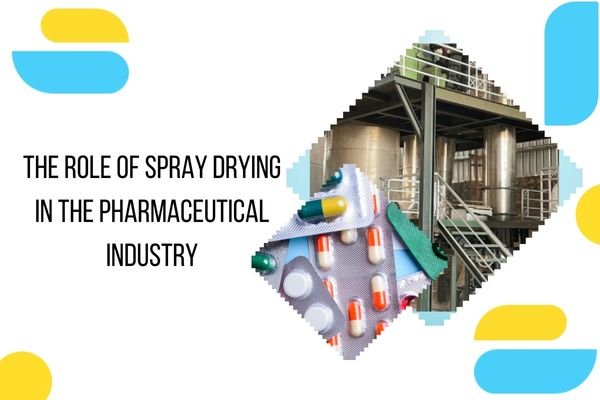
The Role of Spray Drying In The Pharmaceutical Industry Spray drying is a pivotal technique in pharmaceutical manufacturing, converting liquid formulations into fine powders. This process is essential for developing stable, bioavailable, and effective pharmaceutical products. Spray drying involves atomizing a liquid feed into small droplets within a hot drying gas, leading to rapid evaporation and the formation of solid particles. This continuous process efficiently transforms liquids into powders with controlled properties. Spray Drying Applications in Pharmaceuticals Spray drying is employed in various pharmaceutical applications, including: Active Pharmaceutical Ingredients (APIs): Enhancing the solubility and bioavailability of poorly water-soluble drugs. Inhalable Formulations: Producing dry powders for inhalers, ensuring optimal particle size and flow properties. Encapsulation: Protecting sensitive compounds like vaccines, enzymes, and hormones from degradation. Controlled Release Systems: Designing formulations that release drugs at specific rates. Advantages of Spray Drying in Pharmaceutical The benefits of spray drying in pharmaceutical manufacturing include: Uniform Particle Size: Achieving consistent dosing and predictable drug release profiles. Enhanced Stability: Protecting heat-sensitive compounds by minimizing exposure to high temperatures. Scalability: Facilitating the transition from laboratory-scale to large-scale production. Cost-Effectiveness: Offering a continuous process that reduces production costs compared to batch methods. Challenges and Considerations Despite its advantages, spray drying presents challenges such as: Process Optimization: Achieving desired particle characteristics requires precise control of parameters like temperature, feed rate, and atomization pressure. Equipment Costs: Initial investment in spray drying equipment can be significant. Material Compatibility: Ensuring that the process does not adversely affect the chemical integrity of the active ingredients. Conclusion Spray drying is a versatile and indispensable technique in pharmaceutical manufacturing, offering solutions to enhance drug development and delivery. By converting liquid formulations into stable, bioavailable powders, it plays a crucial role in advancing pharmaceutical products.
The Role of Spray Drying In The Food Industry
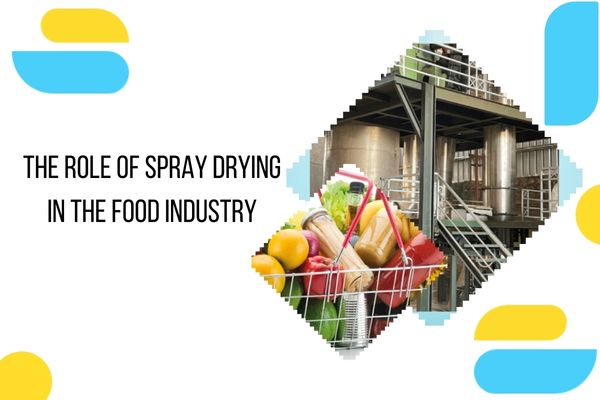
The Role of Spray Drying in the Food Industry Spray drying in the food industry is a process that converts liquid food products into dry powders, improving shelf life, solubility, and preserving nutrients. It is widely used for products like milk powders, coffee, and flavors. The Spray Drying Technology also allows for large-scale, cost-effective production, offering customization in food formulations. Spray dryers ensure the quality of products by preventing microbial growth and maintaining essential nutrients. 1. Extending Shelf Life with Moisture Removal Spray drying effectively reduces moisture levels, preventing microbial growth and spoilage. This extends product shelf life while maintaining essential nutrients, making it a preferred method for dairy, fruit, and vegetable powders. 2. Enhancing Solubility for Instant Products Many food products, such as instant coffee, baby formula, and protein powders, require easy reconstitution. Spray dryer produces fine, uniform particles that dissolve quickly, ensuring consumer convenience and product consistency. 3. Preserving Nutritional Integrity Unlike traditional drying methods, spray drying technology minimizes thermal degradation, protecting heat-sensitive nutrients like vitamins, probiotics, and enzymes. This is essential for functional foods and health supplements. 4. Cost-Effective, Large-Scale Production Spray drying is highly efficient, allowing manufacturers to produce bulk quantities of powdered food products with minimal waste. The ability to transport and store powders easily reduces logistics costs compared to liquid alternatives. 5. Customization and Versatility in Food Formulation Spray drying enables the integration of specialized ingredients such as protein fortifiers, flavor enhancers, and encapsulated nutrients. This process also allows manufacturers to achieve desired particle size, flow properties, and moisture content tailored to specific applications. With its advantages in stability, efficiency, and versatility, spray drying remains a cornerstone of food processing, meeting the evolving demands of the industry while maintaining superior product quality and consumer satisfaction.
Key Components of a Spray Dryer System
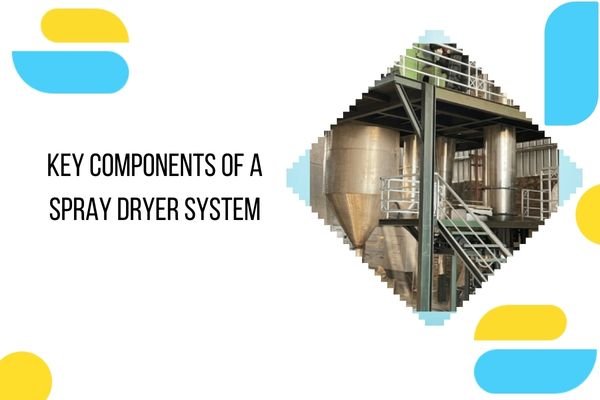
Key Components of a Spray Dryer System A spray dryer is a vital technology used across industries such as food, pharmaceuticals, and chemicals to convert liquid substances into dry powders efficiently. The Spray Dryer Process involves atomization, moisture evaporation, and product collection, ensuring high-quality powder production with minimal product degradation. To maximize performance, understanding the essential components of a spray dryer system is crucial. 1. Feed System: The Starting Point of Efficiency The feed system delivers the liquid material into the drying chamber at a controlled rate. It consists of storage tanks, feed pumps, and pipelines designed for precise flow management. Proper feed system configuration ensures uniform atomization and consistent product quality. 2. Atomizer: The Core of Particle Formation The atomizer plays a pivotal role in breaking down the liquid feed into fine droplets, increasing surface area for efficient drying. Depending on the application, manufacturers use: Rotary Atomizers for high-capacity operations. Pressure Nozzles for uniform droplet distribution. Ultrasonic Nozzles for sensitive materials requiring gentle drying. 3. Drying Chamber: Where Transformation Happens The drying chamber facilitates moisture evaporation by exposing atomized droplets to hot air. Chamber size, shape, and air distribution significantly impact drying efficiency and powder consistency. Optimized chamber design reduces wall build up and ensures uniform drying. 4. Air Heater and Blower: Driving Thermal Energy Hot air is essential for moisture removal. The air heater precisely controls inlet air temperature, while the blower ensures even airflow distribution. Proper temperature management prevents product degradation while maintaining energy efficiency. 5. Cyclone Separator & Bag Filter: Ensuring High Product Recovery Efficient separation of dried particles from exhaust air is crucial. This is achieved using: Cyclone Separators, which use centrifugal force for powder collection. Bag Filters, which trap ultra-fine particles, minimizing product loss. 6. Product Collection System: Delivering the Final Output The dried powder is collected at the bottom of the drying chamber or through cyclone separators. Additional mechanisms such as vibrating sieves or pneumatic conveyors can be used to optimize powder flow and prevent agglomeration. 7. Exhaust System: Ensuring Safety and Compliance The exhaust system effectively removes waste air and residual moisture. It includes ductwork, blowers, and environmental control mechanisms such as scrubbers to meet emission standards and ensure workplace safety. Optimizing these core components enhances product quality, improves energy efficiency, and ensures consistent spray drying performance for industrial applications.
Understanding the Different Types of Spray Dryers and Their Uses
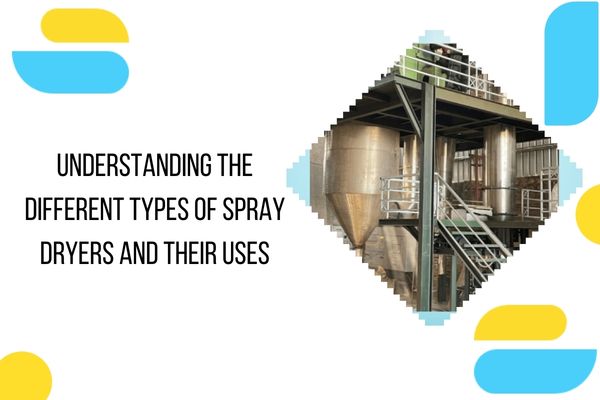
Understanding The Different Types of Spray Dryers and Their Uses In the world of industrial processing, achieving efficiency, precision, and high-quality output is paramount. One of the most versatile and widely used pieces of equipment for transforming liquids into powders is the spray dryer. As a trusted spray dryer manufacturer, we specialize in providing advanced drying solutions tailored to meet the unique needs of various industries. In this blog, we’ll explore the different types of spray dryers, their applications, and how they can optimize your production process. Whether you’re in food production, pharmaceuticals, or chemicals, understanding these systems is essential for making the right investment. Let’s dive in! Types of Spray Dryers 1. Single-Stage Spray Dryers Single-stage spray dryers are the most commonly used type, ideal for applications where the final product doesn’t require extremely low moisture content. These systems are cost-effective, easy to operate, and perfect for industries like food processing, dairy, and detergents. Key Features: Simple and robust design Suitable for heat-sensitive materials Cost-effective for large-scale production Common Uses: Drying milk, coffee, and egg powders Producing detergents and cleaning agents Why It’s Popular: Single-stage spray dryers are widely used due to their simplicity and affordability. They are ideal for industries where moderate moisture content is acceptable, and large-scale production is required. 2. Two-Stage Spray Dryers Two-stage spray dryers combine traditional spray drying with fluid bed drying to achieve lower moisture content and better control over particle size. This type is commonly used in the pharmaceutical and chemical industries, where precision and consistency are critical. Key Features: Enhanced product quality and uniformity Lower residual moisture content Ideal for hygroscopic and heat-sensitive materials Common Uses: Drying pharmaceutical ingredients (APIs) Producing specialty chemicals and food additives Why It’s Popular: Two-stage spray dryers are preferred for applications requiring precise moisture control and uniform particle size. They are particularly useful in industries where product quality is non-negotiable. 3. Three-Stage Spray Dryers Three-stage spray dryers are designed for applications requiring ultra-low moisture content and high powder solubility. They integrate spray drying, fluid bed drying, and static bed drying to produce superior-quality powders. These systems are often used in the production of infant formula, coffee, and specialty chemicals. Key Features: Exceptional product quality with minimal moisture Improved solubility and dispersibility Energy-efficient and cost-effective Common Uses: Manufacturing infant formula and nutritional powders Producing instant coffee and tea powders Why It’s Popular: Three-stage spray dryers are ideal for industries where product solubility and low moisture content are critical. They offer superior product quality and are energy-efficient, making them a cost-effective choice. 4. Closed-Loop Spray Dryers Closed-loop spray dryers are specifically designed for materials that are sensitive to oxygen or require an inert drying environment. These systems recycle the drying gas, making them ideal for solvents, flammable materials, and high-value products like pharmaceuticals. Key Features: Safe handling of flammable or toxic materials Environmentally friendly with minimal emissions Suitable for high-value and sensitive products Common Uses: Drying pharmaceutical intermediates Processing organic solvents and chemicals Why It’s Popular: Closed-loop spray dryers are essential for industries handling sensitive or hazardous materials. They ensure safety, reduce environmental impact, and maintain product integrity. 5. Centrifugal Spray Dryers Centrifugal spray dryers use a high-speed rotating disk to atomize the liquid into fine droplets. They are ideal for producing powders with uniform particle size and are commonly used in the food, chemical, and ceramic industries. Key Features: Uniform particle size distribution High production capacity Suitable for viscous and abrasive materials Common Uses: Producing food powders like spices and flavorings Manufacturing ceramic powders and pigments Why It’s Popular: Centrifugal spray dryers are known for their ability to handle viscous and abrasive materials while producing powders with consistent particle size. They are widely used in industries requiring high production capacity. 6. Nozzle Spray Dryers Nozzle spray dryers utilize high-pressure nozzles to atomize the liquid feed. They are highly versatile and can handle a wide range of materials, including heat-sensitive and abrasive substances. These dryers are widely used in the food, pharmaceutical, and chemical industries. Key Features: Precise control over droplet size Suitable for abrasive and high-viscosity materials Flexible and adaptable to various applications Common Uses: Drying pharmaceutical suspensions Producing food additives and specialty chemicals Why It’s Popular: Nozzle spray dryers are preferred for their versatility and precision. They are ideal for industries requiring control over droplet size and the ability to handle challenging materials. Applications of Spray Dryers Spray dryers are indispensable across a wide range of industries due to their efficiency and adaptability. Here are some common applications: Food Industry:Production of milk powder, coffee, tea, and spices. Pharmaceuticals:Drying of active pharmaceutical ingredients (APIs) and excipients. Chemicals:Manufacturing of detergents, pigments, and catalysts. Ceramics:Production of ceramic powders for advanced materials. Environmental:Treatment of wastewater and sludge. Why Choose Us as Your Spray Dryer Manufacturer and Supplier? As a leading spray dryer manufacturer and supplier, we pride ourselves on delivering cutting-edge drying solutions that meet the highest standards of quality and performance. Our spray dryers are designed with advanced technology to ensure energy efficiency, product consistency, and operational reliability. Our Advantages: Customized Designs: Tailored solutions to meet your specific requirements. High-Quality Materials: Durable and corrosion-resistant construction for long-lasting performance. Comprehensive Support: End-to-end services, from installation to after-sales maintenance. Conclusion Choosing the right spray dryer is crucial for optimizing your production process and achieving the desired product quality. From single-stage systems for basic drying to closed-loop dryers for sensitive materials, each type of spray dryer offers unique benefits tailored to specific applications. Boilers India is here to help you find the perfect solution for your industry. Contact us today to learn more about our spray dryers and how they can enhance your production efficiency.
What is a Spray Dryer and How Does it Work?
What is a Spray Dryer and How Does it Work? When it comes to efficient drying of liquids into powders, few technologies can rival the performance of spray drying. As a spray dryers manufacturer with over 14 years of experience in designing and producing, we understand the intricacies of this innovative process and its immense value across industries. But what exactly is a spray dryer, and how does it work? In this blog, we’ll take you through the basics of spray drying, explain the process in detail, and highlight why it’s such a versatile and efficient solution for transforming liquids and slurries into fine powders. What is a Spray Dryer? A spray dryer is a device used to convert liquid substances into dry powder. It does so by rapidly evaporating the moisture content from the liquid, using hot air and a spray mechanism that disperses the liquid into tiny droplets. This process is ideal for heat-sensitive materials, as the drying happens quickly and efficiently, minimizing degradation. Spray dryers are commonly used in industries like food, pharmaceuticals, chemicals, and even materials science, where the need for powdered products is high, and moisture control is critical. How Does a Spray Dryer Work? At the core of the spray drying process is a combination of atomization (breaking the liquid into small droplets) and rapid drying in a hot air stream. Here’s a step-by-step breakdown of how it works: Liquid Feed Preparation: The process begins with preparing the liquid feed, which could be a solution, suspension, or slurry. This feed is typically made to a specific concentration, depending on the desired final powder characteristics. In industries like food manufacturing, for example, a liquid might be a mixture of milk or fruit juice. Atomization: The liquid feed enters the spray dryer and is introduced into the atomization chamber. This is where the magic happens. The liquid is dispersed into fine droplets using one of several atomization methods: Nozzle Atomizers: The liquid is forced through a nozzle, creating a fine mist of droplets. Rotary Atomizers: A high-speed rotating disk breaks the liquid into tiny droplets. Contact with Hot Air: The fine droplets are then introduced into a chamber filled with hot air, typically ranging from 150°C to 300°C (depending on the material being dried). The hot air flows in a specific direction to maximize drying efficiency and ensure rapid evaporation. Evaporation: As the droplets fall through the hot air stream, the moisture within them evaporates quickly, leaving behind dry particles. This is where spray drying excels—its speed allows for the efficient drying of heat-sensitive materials with minimal thermal damage. Powder Collection: After the droplets have been dried into powder, the dry particles are separated from the air stream using a cyclone separator, a bag filter, or a combination of both. These systems capture the fine powder, which is then collected for further processing or packaging. Final Product: The result is a fine, free-flowing powder, which can be used as an ingredient or finished product in a variety of industries. Depending on the material, spray drying allows for the retention of nutrients, active ingredients, and other key qualities. Why Choose Spray Drying? Spray drying offers a range of benefits, especially when compared to other drying methods like freeze-drying or tray drying. Here are some of the reasons why spray drying is the go-to choice for manufacturers with over a decade of experience in the field: Speed and Efficiency: Spray drying is incredibly fast compared to other drying techniques. This means that large quantities of liquid can be converted into powder in a relatively short time, making it ideal for high-volume production. Heat Sensitivity: Many materials, especially in the food and pharmaceutical industries, are heat-sensitive. Spray drying offers a way to dry these materials quickly without causing excessive thermal degradation, retaining nutrients and active compounds. Particle Size Control: The spray drying process allows for precise control over the size and shape of the powder particles. This is critical for applications where uniformity is key, such as in pharmaceuticals and food products. Versatility: Spray dryers can handle a wide range of feed materials, from food and dairy products to chemicals and pharmaceuticals. This versatility is why they are used across many industries. Scalability: Spray drying systems are highly scalable, making them suitable for both small-scale lab applications and large-scale industrial production. Conclusion With over 14 years of experience in manufacturing spray dryers, we have seen firsthand how this technology has transformed industries and helped businesses deliver high-quality powder products efficiently and effectively. Whether you are in the food, pharmaceutical, or chemical industry, spray drying offers numerous advantages—speed, efficiency, and precision control over the drying process. If you are considering integrating spray drying into your production process or need a custom-designed spray dryer, our team is equipped to provide you with the expertise and equipment tailored to your needs. Spray drying is an investment in quality, and with the right system in place, the results speak for themselves.